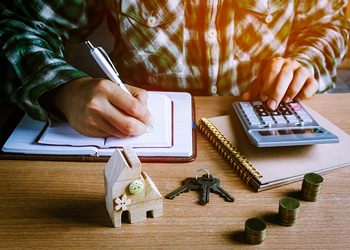
Understanding Window Costs and Financing Options
Replacing old windows is a major home improvement project that requires careful planning and budgeting. While replacing windows can significantly improve energy efficiency and comfort, the upfront costs need to fit within your budget.
There are several factors that determine the overall price of new windows. The good news is there may also be financing options or rebates available to help offset some of the expense. Let’s take a closer look at the key factors affecting window costs and your financing alternatives.
Factors Impacting Window Costs
Window Size
Window size is a major determinant of cost, as larger windows simply require more glass, framing materials and labor to produce and install. When collecting quotes, it’s important to provide accurate measurements of each window opening so contractors can price their bids appropriately.
Ideally, measure the wall opening from inside the window casing or framing. Jot down the length and width in inches of every window that needs replacing to the nearest 1/4 inch. Then calculate the total square footage by multiplying length by width and dividing by 144 (there are 144 square inches in a square foot).
For bay or bow windows with multiple pane sections, you’ll need to add up the square footage of each component. Don’t just sketch the overall dimensions, as installers will need to order individual window units.
It’s also a good idea to confirm with contractors if their quoted prices assume removing and disposing of the old windows, or if that will be an additional line item cost. Proper removal and disposal of hazardous materials like lead glass must be handled professionally.
By taking precise window measurements and clearly communicating your project details, you’ll receive the most accurate estimates of total project costs up front based on material requirements and installation labor. This prevents surprises and helps ensure your window replacement budget is sufficiently allocated
Material
The type of material used to construct a window frame has a significant impact on both its performance and pricing. Vinyl is typically the most affordable option and a good choice for replacement projects on a budget. However, its longevity is less than other materials. Standard vinyl frames without additional weatherstripping or glazing also tend to have higher U-factors.
Fiberglass windows offer improved insulation values over basic vinyl but come at a higher starting cost, sometimes comparable to wood. Look for fiberglass frames branded as rot-resistant and requiring no annual maintenance for the best long-term value. High-performance models utilize chambers, spacers and glazing systems for top energy efficiency.
Wood windows provide a beautiful, traditional aesthetic but need frequent refinishing or replacing of components to prevent rot over 20-30 year lifetimes. Premium teak or cedar holds up better but is extremely expensive. Aluminum is a durable yet poor insulator often used for commercial applications instead of residential.
Custom wood styles with intricate muntin patterns or unusual shapes can routinely run $1,000-$2,000 or more per window depending on detail level. For most replacement projects, balancing material quality and eco-friendliness with affordability is ideal. Fiberglass usually hits that sweet spot.
Window Type
Different window types have varying engineering requirements and complexities that affect their costs. Simple double-hung windows with two sashes that slide up and down vertically are typically the most affordable option. They have a straightforward design and operation that doesn’t require complex engineering.
Casement windows, which open along side hinges, require more intricate hardware and sealing to keep them weather-tight when closed. The crank mechanisms and hinges also add to casement window costs.
Awning windows are hinged at the top and open outward. Like casements, they require careful engineering of the hinge and sealing system to prevent air and water infiltration when closed.
Their crank handles and arms also make them more complex than basic double-hung windows.
Bay windows are composed of three separate windows joined together to project outward from a wall. The angle of the side windows and integration of the windows into a cohesive unit requires precise engineering and framing. The complexity adds expense compared to regular windows.
Specialty window shapes like rounds, arcs, triangles or trapezoids require custom-engineering and fabrication since they deviate from standard rectangles. Their unique curvatures, angles and sizes demand precision cutting and assembly. This custom work raises their costs compared to common rectangular window designs. In summary, basic double-hung windows tend to be the most economical, while casements, awnings, bays and custom shapes require extra engineering and customization that increases their costs.
Glass Options
The glass used in windows significantly impacts their price. Basic single pane clear glass is the most affordable option. It offers no insulation value but allows full light transmission. For better energy efficiency and noise reduction, double or triple pane insulated glass units can be used.
This type has two or three panes separated by air or gas filled spaces. Adding special coatings like low-emissivity (low-E) films further reduces heat loss and gain. Low-E glass costs more than regular clear double pane units. Insulated units can also be filled with argon or krypton gas between panes to increase efficiency.
However, argon and krypton cost more than air filled units. Tempered glass is treated with heat to increase strength and shatter-resistance. These specialty treatments add expense over regular glass.
Laminated glass has a plastic interlayer sandwiched between glass sheets for security and safety. The lamination process increases costs over single pane glass. In summary, while basic single pane glass is cheapest, double or triple insulated units with low-E, tempering, lamination or gas fills substantially increase cost for improved performance and durability. The highest efficiency coated gas-filled triple pane glass can cost up to 5-10 times more than single pane.
Hardware Finishes
Hardware finishes substantially influence window costs. Basic painted aluminum hardware in standard colors like white or black is the most affordable option. However, specialty finishes like bronzed, antique brushed or oil-rubbed bronze aluminum cost more since they require additional finishing steps.
Solid brass hardware adds a significant upcharge over aluminum due to the higher material cost. Brass also comes in different finishes like satin, polished or antique which range in price. Other upscale hardware options like wrought iron, pewter or copper carry premium prices over standard aluminum.
Hardware finishes should coordinate with the window color and style for a cohesive look. Opting for custom or specialty hardware finishes to match the window aesthetic can require pricey upcharges. To keep costs down, choose standard painted aluminum hardware in white or black rather than upscale brass, bronze or antique finishes.
Matching basic hardware to window color is easier and more budget friendly than trying to coordinate special metal finishes across all windows.
Frames and Trim
Windows with ornamental trim, grill patterns or premium exterior cladding materials tend to be pricier. Custom sizing can also boost costs.
Energy Efficiency
High-performance windows rated with lower U-factors and solar heat gain coefficients command higher prices but save significantly on utility bills over time.
Other Factors
Installation complexity, accessibility to the window area, warranty options, accessory items like screens may also influence final pricing. Getting multiple quotes is wise.
Average New Window Costs
Considering these factors, here are some typical price ranges to reference:
Basic vinyl double-hung replacement windows: $150-250 per window installed
Energy efficient vinyl windows with low-E glass: $250-400 per window
Fiberglass windows: $300-600 per window
Wood windows: $500-1,000+ per window
Specialty shapes: $800-2,000+ per window
On average, expect to pay $300-700 per window to get energy-efficient vinyl, fiberglass or custom windows installed by a professional. Window replacement projects can cost $5,000-25,000 depending on the home’s size.
Financing Options for Window Replacement
Given the substantial costs involved, financing window projects is commonly considered. Here are some options to explore:
Home equity line of credit – Borrow against your home’s equity at competitive interest rates.
Personal loan – Unsecured personal loans through banks allow 3-5 years to repay at fixed rates.
0% financing from retailers – Major retailers like Andersen, Pella may offer no-interest financing for 12-60 months.
State and local rebates – Check incentives offered through energy companies or governments.
Federal tax credits – Residential energy efficiency tax credits were recently expanded.
Window manufacturer rebates – Companies like Window World provide cash back for replacements.
When financed responsibly, options like home equity or 0% retail financing can make the investment in energy efficient windows affordable through low monthly payments and the savings realized down the road. Be sure to compare terms carefully between offers.
In Summary
There are many variables impacting window costs. Always get competitive quotes to find quality products that fit your budget. Federal tax credits and local energy rebates help defray some of the initial expense for higher efficiency upgrades.
Financing tools allow projects to be paid over time out of pocket savings from lower utility bills. With careful planning and smart purchasing decisions, you can invest in durable, energy saving windows for your home while optimizing long-term financial incentives. Proceed knowledgeably to achieve both comfort and cost-effectiveness from your window replacement project.